Electrical Safety Gloves Explained
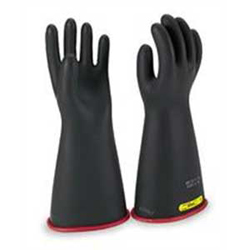
Personal protective equipment (PPE) is important to keeping electrical workers safe when working on electrical equipment. One important piece of electrical safety equipment is rubber insulating gloves. Electrical safety gloves must have a combination durability and flexibility, along with physical strength and high dielectric qualities in order to be effective.
An electrical safety glove system might include:
- Rubber insulation gloves (classified based on level of protection and voltage)
- Leather protector gloves (worn on top of rubber insulation gloves to prevent cuts, scratches, and punctures)
- Liner gloves (lowers the rubber insulation glove discomfort; also absorbs sweat during the warm seasons and provides warmth in the cold seasons.)
Electrical Safety Gloves – Understanding Electrical Safety Glove Classifications
Electrical safety gloves are categorized by a voltage protection level and their resistance to ozone. The Occupational Safety and Health Administration (OSHA) gives specific requirements for glove design, in-service care and usage in a standard known as the Electrical Protective Equipment Standard. This electrical safety standard also provides requirements for not only gloves, but matting, insulation blankets, sleeves, line hoses and covers.
OSHA classifies voltage level using numeric classes:
Class Number: 00
- Maximum Voltage Use: 500 volts
- A/C-proof Tested: 5,000 AC volts
Class Number: 1
- Maximum Voltage Use: 7,500 volts
- A/C-proof Tested: 10,000 AC volts
Class Number: 2
- Maximum Voltage Use: 17,000 volts
- A/C-proof Tested: 20,000 AC volts
Class Number: 3
- Maximum Voltage Use: 26,500 volts
- A/C-proof Tested: 30,000 AC volts
Class Number: 4
- Maximum Voltage Use: 36,000 volts
- A/C-proof Tested: 40,000 AC volts
Electrical safety gloves are also classified in “type” categories for ozone resistance. Type 1 electrical safety gloves are non-ozone resistant and Type II electrical safety gloves are ozone resistant.
Electrical safety gloves are among the most important articles of personal protection for electrical workers. To be effective, electrical safety gloves must incorporate high dielectric and physical strength, along with flexibility and durability. For superior performance they should meet and/or exceed the requirements of current American Society for Testing and Materials (ASTM) D120 specifications. Gloves should also be electrically tested following ASTM D120/IEC903 specifications.
Electrical safety glove systems usually consists of:
- Rubber Insulating Gloves — Classified by the level of voltage and protection they provide.
- Liner Gloves — Are used to reduce the discomfort of wearing rubber insulating gloves in all seasons, for year round use. Liners provide warmth in cold weather, while they absorb perspiration in the warm months. These can have a straight cuff or knit wrist.
- Leather Protector Gloves — Should always be worn over rubber insulating gloves to provide the mechanical protection needed against cuts, abrasions and punctures. Look for those that are steam pressed on curved hand forms to ensure proper fit over rubber gloves.
ELECTRICAL SAFETY GLOVES - CLASSIFICATION
Employees who work in close proximity to live electrical current may require a variety of electrically insulating protective equipment. The Occupational Safety and Health Administration (OSHA) outlines this in their Electrical Protective Equipment Standard (29 CFR 1910.137) which provides the design requirements and in-service care and use requirements for electrical-insulating gloves and sleeves as well as insulating blankets, matting, covers and line hoses.
Electrical safety gloves are categorized by the level of voltage protection they provide and whether or not they’re resistant to ozone. Voltage protection is broken down into the following classes:
For electrical safety gloves, ozone resistance is covered by the “Type” designation. A Type I glove is not ozone-resistant, while a Type II is ozone-resistant.
Once the electrical safety gloves have been issued, OSHA requires that “protective equipment shall be maintained in a safe, reliable condition”. This requires that gloves be inspected for any damage before each day’s use. Electrical safety gloves must also be inspected immediately following any incident that may have caused damage.
OSHA requires that insulating gloves be given an air test along with the inspection.
INSPECTION
In order to maintain the highest level of insulating protection and ensure long life, it is essential that electrical safety gloves (and sleeves) are properly cared for and stored.
Before each use, electrical safety gloves and sleeves should be inspected for holes, rips or tears, ozone cutting, UV checking and signs of chemical deterioration. Refer to ASTM F 1236, Standard Guide for Visual Inspection of Electrical Protective Rubber Products for Additional Information.
Electrical safety gloves and Sleeves should also be examined to determine if they show any damage as a result of chemical contamination, particularly from petroleum products. The first sign of exposure is swelling in the area of contamination. Should any rubber equipment be exposed to chemical contaminants or be suspect of any other physical damage, it should be turned in for inspection, cleaning and electrical testing.
Since sleeves cannot be inflated, they are inspected along the edge as they are rolled. Rolling will stretch the sleeve along the edge, making cuts, tears and ozone cutting more visible. After the outside of the sleeve is inspected, the procedure should also be repeated with the sleeve turned inside out.
COMMONLY ASKED QUESTIONS
Q. Can I just use the rubber electrical safety gloves only, and not have to buy the leather part?
A. A leather protective glove should always be worn over rubber insulating gloves to provide the needed mechanical protection against cuts, abrasions, and punctures.
Q. Would re-testing be needed if I don’t use the gloves very often and visually see no damage?
A. Yes, re-testing is still needed to verify the integrity of the material and to ensure electrical safety is maintained for the user.
Q. If I find a hole, can I just “patch it” - like a tire inner tube?
A. No - because this would not comply with ASTM or OSHA Standards for Electrical Protective Gloves, and it would not pass Accredited Laboratory Testing.
- Read More Here: Arc Flash and Electrical Safety
- Read More Here: Electrical Safety Training
- Read More Here: Electricity
For more information, see:
On-site training
Interested in cost effective, professional on-site electrical smart grid training?
We can present an On-site Training Course to your electrical engineering and maintenance staff, on your premises, tailored to your specific equipment and requirements. Click on the link below to request a FREE quotation.
Live Online Electrical Training Schedule
September 2025
- UPS System Training
- Arc Flash Training - CSA Z462 Electrical Safety
- Reading Electrical Schematics Training
- 2024 CE Code - Changes and Fundamentals
- 2024 CE Code - Combined Course: Changes/Fundamentals and Calculations
- Grounding and Bonding and The NEC - Section 250
- Combined NFPA 70e LV Arc Flash And HV Electrical Safety
- NFPA 70e Training
- High Voltage Safety Training
- Industrial Electricity Basics
- CE Code Calculations: Practical Applications and Advanced Techniques
- VFD Training
Arc Flash Group Training

We can present this Course to your electrical engineering and maintenance staff, on your premises, tailored to your specific equipment and requirements. We are ready to help design this program for you. Click on the link below to request a FREE quotation.